Oxford Brookes University recently published a paper on using H-shape vertical axis wind turbines in wind farms and believes that it might be the future.
Table Of Content
- Computer Simulation
- Performance Augmentation
- No wind mixing
- Massive instantaneous leap
- Vertical-vs. horizontal-axis turbines
- Conclusion
- FAQ
- You May Also Like
- External Links
Research that was only just completed and published by Oxford Brookes University reveals that “conventional propeller-type” wind turbines, or HAWTs, in wind farms might be outperformed by H-shape Darrieus vertical-axis turbines (VAWTs) if they were built in a certain manner.
According to a press release issued by an institution headquartered in the United Kingdom, VAWTs may boost each other’s performance by up to 15% when they are tightly interspaced in pairs. This story generated a lot of media interest. An article in the May issue of the business magazine Forbes said that a new discovery made by engineers at Oxford Brookes University’s School of Engineering, Computing, and Mathematics could change the design of offshore wind farms for good.
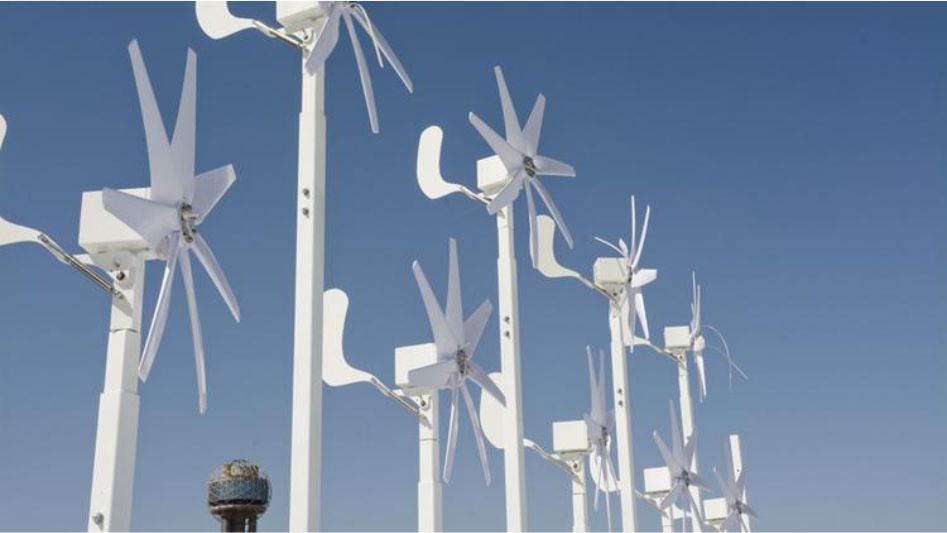
But how accurate are the forecasts that may be gleaned from two-dimensional modeling of hypothetical VAWTs with 20-meter rotors in comparison to the “conventional” offshore giants that are in use today? Who will be responsible for their creation and development?
Computer Simulation
The research article titled “Numerical modeling and optimisation of vertical-axis wind-turbine pairs: A scale-up approach” was first distributed by Elsevier as part of their Renewable Energy publication in the month of March. According to reports, it is the first study of its kind to do a complete analysis of many factors affecting wind turbine performance. These characteristics include array angle, direction of rotation, turbine spacing, and number of rotors.
For the purpose of conducting the in-depth investigation, the university’s research team, directed by Iakovos Tzanakis, a professor in technology, design, and the environment, used comprehensive computer simulation. Tzanakis said that the findings of this research show that vertical wind farms are the way of the future for the industry. Wind turbines at vertical-axis wind farms may be built to be much closer to one another, which boosts their overall efficiency and, as a result, brings down the cost of producing power. In the long term, the use of VAWTs has the potential to hasten the greening of our energy systems, resulting in a greater proportion of renewable energy sources providing clean and sustainable energy.
The researchers contend that VAWTs in wind farm arrays do not experience the HAWT-related turbulence wake concerns that are caused by the first row. These issues cause the production of the rows of turbines behind them to fall by up to 40%. They think that if we used machines with a vertical axis instead of a horizontal one, we could get rid of this problem and make the VAWTs work better together.
The investigation made use of two rotors of comparable dimensions, with the second rotor being positioned a distance downstream equal to three times its diameter. The second rotor was positioned at a 60-degree array angle (ß) to the predominant wind direction, which resulted in the greatest gain in power production when compared to two units that were each working in isolation. This was accomplished by positioning the array at an angle of ß.
Allowing the two rotors to either co-rotate in the same direction or counter-rotate was another variable that the team decided to test. The results showed that the counter-rotating pair worked better, but only at lower array-angles of around-30 to +30 degrees. When the wind blows directly over the two rotors that are lined up with the direction the wind usually blows, the power output is at its lowest (0 degrees).
Last but not least, a two-dimensional space is a fundamental component of computational fluid dynamics (CFD) modeling.
Performance Augmentation
For the purpose of the study, the team decided to use an H-type Darrieus rotor shape with a 20-meter rotor diameter. The lead author, Joachim Toftegaard Hansen, explained why the team made this decision: “Other studies have verified similar performance augmentations for other Reynolds numbers [to predict flow patterns, too.” The consequences of turbine size are something that we may be interested in analyzing in our future research, and this is something that we are perhaps interested in researching.
Whether or not VAWT-based offshore wind farms could drive themselves at the same level as the most recent HAWT-technology, which is now operating at the 11-15 MW scale and has a total of 30 years of accumulated marine expertise under its belt, is an important one.
A specialist in aerodynamics, Jens Nrkaer Srensen is a professor in the department of wind energy at the Technical University of Denmark (DTU). He has previously worked with vertical axis wind turbines (VAWTs). He disputes the scientific design foundation of the study endeavor conducted at Oxford Brookes, as well as the design setup and the findings used to support the conclusions.
“I would want to focus my criticisms on three primary topics. The first concern is over the usage of a form that has only two dimensions in the CFD flow model. Because the mixing of fresh high-energy wind from the upper, outer layers with “depleted-energy” wind flow inside the wind-farm boundaries is of key importance to continuously regenerating energy for generation in downstream turbine rows, I believe that wind flow in a wind farm array should always be studied from a three-dimensional perspective.
Because the spinning blades “sweep” new air from higher wind layers into the array during each rotor rotation, this vital mixing of wind flow inside wind farms with HAWTs takes place automatically. This is an important aspect of how wind farms with HAWTs work. The newest and biggest offshore turbines already reach heights of up to 250 meters at the tip, and they will soon reach heights of up to 300 meters and even higher. At these elevations, the wind speeds, and therefore the amount of energy in the wind, are quite high.
No wind mixing
Sörensen says that vertical axis wind turbines (VAWTs) have rotors that constantly spin in the same plane because the rotating axis of the rotor is vertical in these turbines. As a consequence of this, there is no mixing of new wind flow with wind flow that has already been “drained of energy,” and this “used” air stays within the wind farm array, having a significant detrimental effect on the potential power output in all additional rows downstream.
His second point of contention is with the configuration of the study, which consisted of just two rotors. As stated in the paper, these are “positioned in a rotating zone inside a wider rectangular domain with immovable walls at top and bottom, a velocity entrance, and a zero-gauge pressure exit,” as stated in the paper. The following diagram, which comes from the study, shows the best configuration, which has two turbines, and the flow boundary conditions.
R1 was always revolving in a direction that was counter-clockwise, but the direction of rotation of R2 changed depending on whether or not the pair was co-rotating. “dist” referred to the distance between the turbines, while “” denoted the array angle.
Srensen says that this broad approach to research has a lot of other basic design problems that need to be fixed.
My third criticism is that it overlooks real-life characteristics that are present inside a wind farm, where such ideal parameters as uniform wind flow and one-sided wind direction do not occur. He says that a major flaw in the way the system was studied and designed is that it doesn’t take into account how the wind flow interacts with other rows of turbines further downstream.
“Taking into consideration all of these defects and inaccuracies, the stated advantage of up to 15% power augmentation for closely interspaced VAWTs in wind-farm arrays seems to be exceedingly implausible,” adds Srensen. “This benefit is claimed for VAWTs in wind farms that are closely spaced.”
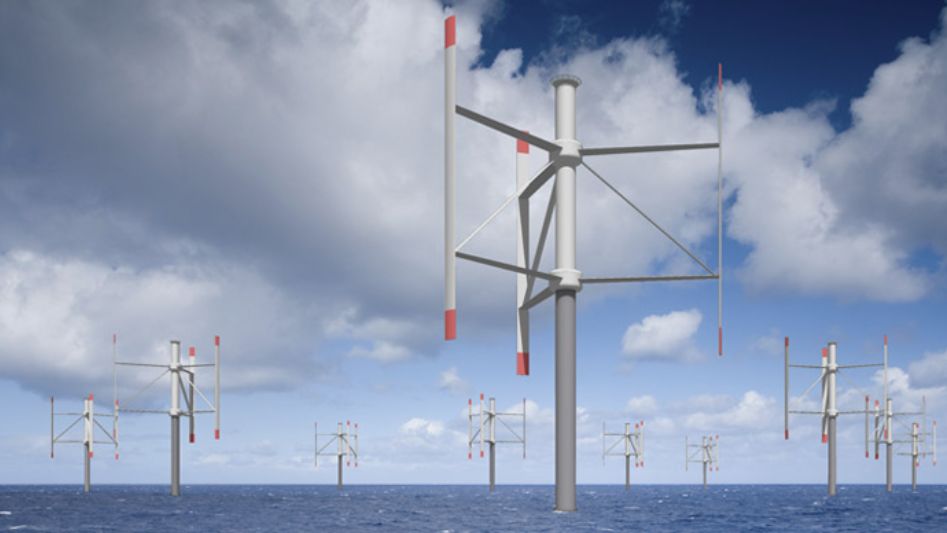
Because of their better aerodynamic efficiency, high-altitude wind turbines (HAWTs) may be placed considerably closer to one another in wind farms than other types of turbines. As a result, HAWTs give a much larger yield per area than VHTs (see Vertical-versus horizontal-axis turbines). He comes to the conclusion that power production with the lowest lifetime cost of energy (LCoE) is still essential.
Massive instantaneous leap
The research didn’t look into how to bring VAWT technology up to the level of current HAWT technology, but it’s likely to be hard and full of obstacles (see) and unknowns.
In 2009 and 2010, two businesses in the United Kingdom, Vertax Wind and Wind Power’s Aerogenerator X (below), proposed plans for offshore-dedicated 10MW VAWTs; however, none of these concepts made it to the prototype stage. Both designs have very high specific power ratings. The Vertax 10MW design has a rotor diameter of 140 meters and a blade length of 110 meters, and the Aerogenerator X design has a specific power rating of about 1,050W/m2.
A picture of a windmill and something else outside, with a description that was made by a computer.
In contrast, the HAWT-type Siemens Gamesa SG 11-200 DD has a power density of 350 watts per square meter, while the SG 222 DD (in 14 MW mode) has a power density of 362 watts per square meter.
In order to build vertical-axis turbines into full-scale competitive commercial ideas matching the newest and biggest 12-15MW HAWT flagship category, technological firms are essentially beginning with a track record obtained mostly with kilowatt-class turbines and typically only limited onshore experience.
Such all-encompassing product development procedures will call for a significant instantaneous scaling leap in wind technology as well as a significant increase in industrialization effort. To take it to completion and then fast-track it to commercial ramp-up, leading to bankability and beyond, it also needs major, powerful partners with a long-term commitment and significant funds.
Vertical-vs. horizontal-axis turbines
One of the main advantages of vertical-axis wind turbines (VAWTs) over their horizontal counterparts (HAWTs), which are used upwind, is that they can catch wind from all directions without needing a yaw mechanism.
When compared to contemporary, large-scale HAWTs, these older models have a substantially lower aerodynamic efficiency. This is the primary drawback. The paper from Oxford Brookes University cites a maximum pressure coefficient (Cp) in the range of 35–40%, whilst the HAWT report says approximately 50% for turbines running in isolation. The design aim for their product (seen below) cites a Cp of 38–39% as the design goal.
A line of windmills standing in the middle of a whiteout. Description automatically created with poor confidence.
Because of their decreased aerodynamic efficiency, VAWTs must have a much lower specific power if they are to produce the same amount of energy as conventional wind turbines. This is one of the key consequences. This means that there is a fundamental need to fit a larger rotor per megawatt within the same wind classes they are designed for and the necessary yearly full load hours.
Some designs of VAWT do not have a self-starting capability, which necessitates the use of an external power source (with the accompanying loss of energy) during each starting-up operation. This power source could be a generator-motor electric machine with two modes or two separate devices.
In the past, non-self-starting small-scale VAWT rotors were sometimes outfitted with a Savonius drag-type rotor on the inside, but this was always done at the cost of the overall aerodynamic efficiency of the system.
Controlling the power output is another one of the challenges presented by VAWT:
- One of the output control options that may be used in stall-type variable-speed designs with a fixed blade angle is rotor-speed control. This allows for a dual-mode generator motor to maximize and maintain the rated output level. The absence of an aerodynamic braking mechanism in current pitch-controlled HAWTs is considered by some industry professionals to be the most significant drawback, as well as a potential safety risk (three independent fail-safe aerodynamic brakes). One problem that is connected to another is that constant switching of the load direction when the turbine is operating in the range of power for which it was designed might hasten the fatigue of the materials and cause failures to occur prematurely.
- An alternate method is to use pitchable blades, in which case each blade would be fastened to support arms and bearings in order to enable it to spin. When compared to HAWTs, this necessitates the use of at least one or more bearing supports and pitch systems for long blades, which results in an increase in complexity, capital expenditures, and most likely operational expenses as well. This is due to the fact that the bearings and pitch systems are positioned in areas that are difficult to reach and are exposed. They might be placed at a distance of around 110 meters from the center of the rotor in a hypothetical 11 MW H-type Darrieus turbine that has a rotor diameter of 220 meters, blades that are 175 meters long, and a power rating of 286 W/m2.
- A third obstacle is that the complete VAWT-rotor aircraft is always oriented in such a manner that it faces straight into the wind. An elaborate and expensive braking mechanism is required in order to stop the plane and lock the rotor when the wind speed is strong. Previous attempts to construct H-type Darrieus turbines with reefable or foldable rotors failed either because they were too expensive or for other reasons, such as rapid wear in the pivot points as a result of, among other things, lubrication challenges, which resulted in imbalances, vibrations, and premature failures. Efforts to build these kinds of turbines are being redone with rotors that can be folded or twisted.
Conclusion
Vertical axis wind turbines, despite the fact that they generate far less power than horizontal turbines, are nevertheless capable of generating electricity and, depending on the context, may be the superior choice. They provide fewer obstacles and dangers to maintain and are better suited to environments with a restricted amount of available space. This design has continued to be popular despite the obstacles that it presents, since engineers have discovered uses for it in small-scale installations, especially in urban locations. There is a chance that, as technology improves, VAWTs will be able to produce energy more efficiently and offer more benefits when used in different ways.
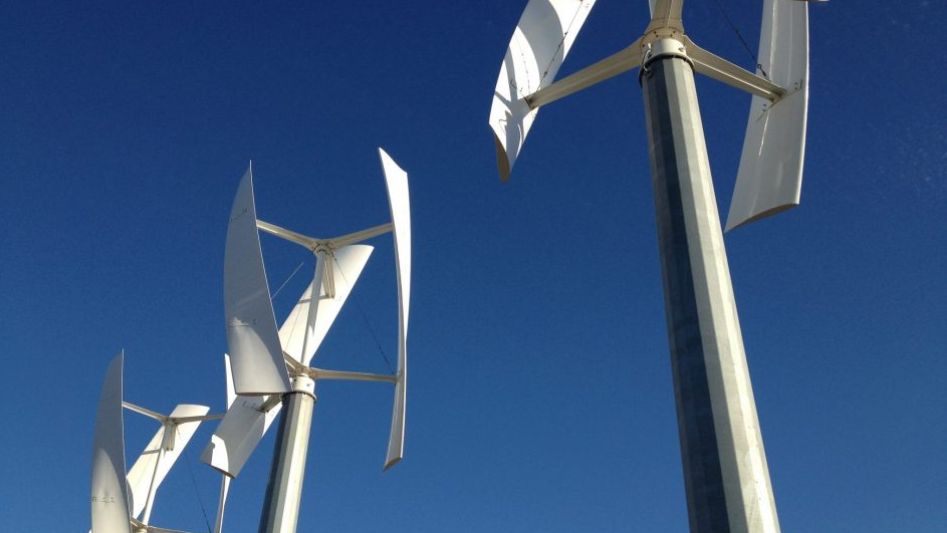
FAQ
Why aren’t wind turbines with a vertical axis utilized more often?
Because not all of the blades create torque at the same time, the production of energy using vertical systems is not as efficient as using horizontal systems. The other blades are moved along by just being pushed. When the blades are rotating, there is a greater amount of drag on them.
Are wind turbines with a vertical axis more efficient?
This enables wind turbines with a vertical axis to produce energy even in conditions when the incoming wind is relatively feeble. Even though a wind turbine makes much less power when the wind is blowing slowly than when it is blowing quickly, it is still better to have a wind turbine that can collect even slow winds.
Where do you see wind turbines going in the future?
The market for renewable energy technologies is expanding at an exponential rate, and technological advancements in wind turbines are responsible for a significant share of this expansion. According to the results of recent research, it looks like wind power will be the most cost-effective way to make electricity in the near future.
You May Also Like
- What Is A Vertical Axis Wind Turbine (VAWT)?
- What Are Wind Turbine Blades Made Of? Could They Be Recycled?
- Wind Turbines For At Home: Benefits and Challenges
- Vertical Axis Wind Turbines Will Dominate The Floating Offshore Wind Market
- What Is The Swept Area Of A VAWT?
External Links
- FUTURE OF WIND TURBINE TECHNOLOGYthe future
- 7 ADVANTAGES OF VERTICAL AXIS WIND TURBINES (VAWT)
- Vertical Axis Wind Turbines Advantages & Disadvantages
- Vertical turbines could be the future for wind farms
- Are Vertical Turbines The Future For Wind Farms?