Dimpled Blade Design (Golf Balls Effect)_Passive Flow Control
At WindCycle we research and develop technologies to improve the design and efficiency of VAWT by using Passive Flow Control (PFC) techniques to increase the lift force and the corresponding torque of the turbines.
The goal is to enhance turbine efficiency by using passive techniques where no energy needed to control the flow separation like moving flaps, DBD…etc.
Design features:
This turbine version has a high lift low Reynolds number airfoil to allow starting at low wind speed.
The straight blade has a pattern of dimples on the suction side. The dimples built like the dimples on the golf ball. Several studies confirmed that dimples on golf ball increase the lift and reduce the drag due to the delayed boundary layer separation unlike smooth undimpled surfaces.
Dimensions:
Rotor Diameter(m) | 0.5 |
Rotor Tall (m) | 1.0 |
Swept Area (m2) | 0.5 |
Overall Height | 1.56 |
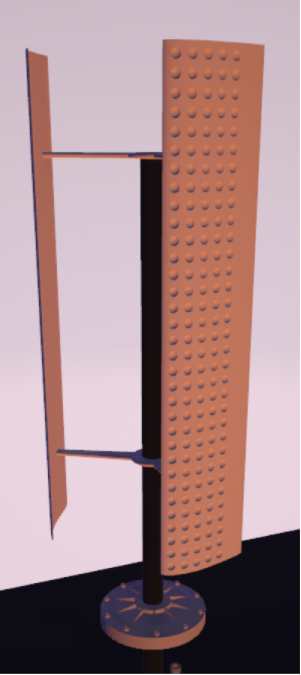
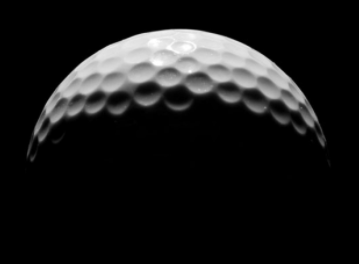
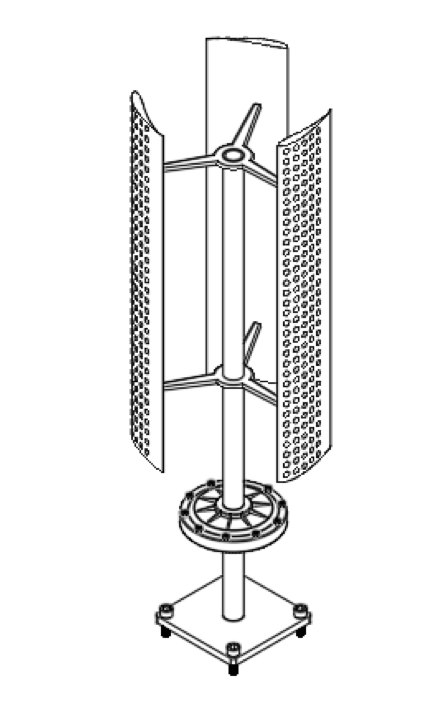
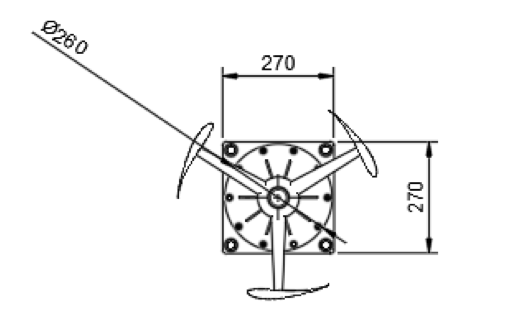
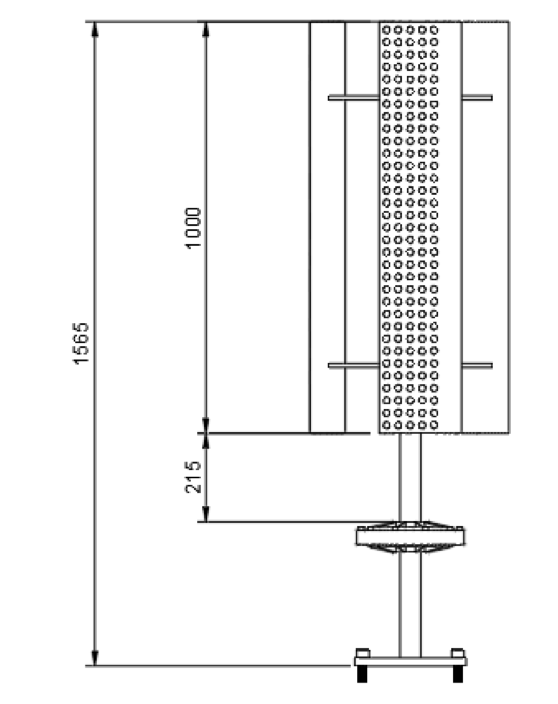
Expected Performance:
Increased performance by modifying airfoil surface topology using dimples has been proven by several studies. An experimental work conducted at Ohio university by Lake JP [1] postulated that using dimples in a vane of low-pressure turbine results in loss reduction ranging from 5.1% at 100K Reynolds number to 51.7% at 50K Reynolds number. Other CFD study conducted by Arun K.K et al. [2] presented that a performance increased by 14.7% in dimpled blade compared to plain blade.
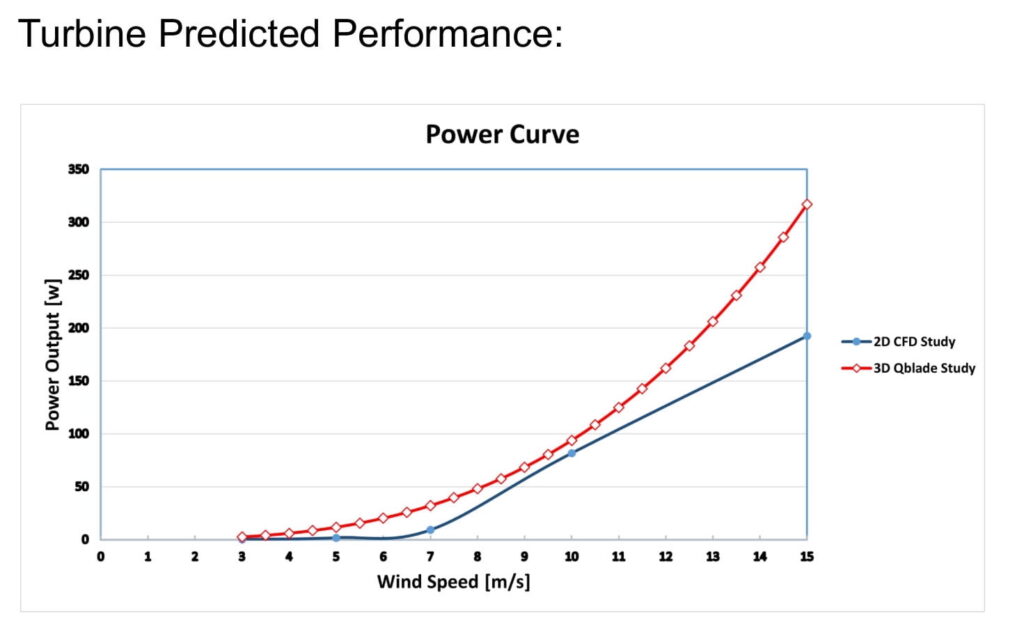
References
- Lake JP. Flow separation prevention on a turbine blade in cascade at low Reynolds number. PhD thesis. Ohio: Air Force Institute of Technology; 1999
- Rajagopal, Ajay & Kumar, Sam. (2018). Analyzing the Effect of Dimples on Wind Turbine Efficiency Using CFD. International Journal of Applied Engineering Research.